This composite part consists of Terminal-1,Terminal-2, Magnetic Bushing, Stator, Plastic Stem. The manufacturing Process is Plastic
Injection Molding(stem) -> Plastic Injection Molding Assembly
(Terminal-1,Terminal-2, Magnetic Bushing) -> Joining the Assembly,
Stator, Stem. | 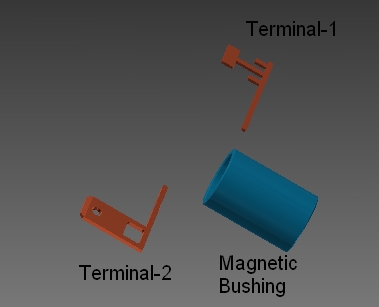 |
Use the plstic injection molding to combine Terminal-1, Terminal-2, Magnetic Bushing and Bobbin. Here one plastic mold. | 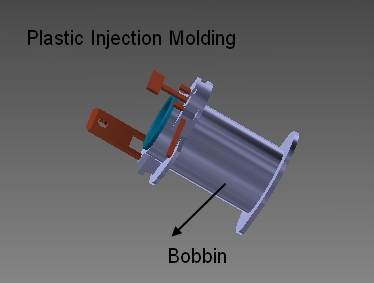 |
Here
do another plastic injection molding part - stem first. Here another
plastic mold. And then making the joining to combine these parts - that
part in last figure, stator, and stem. Here produces a geometrical
tolerance problem - eccentricity and has a defective rate around 20%
due to the joinging. This problem causes a oil leak and higher pressure drop. | 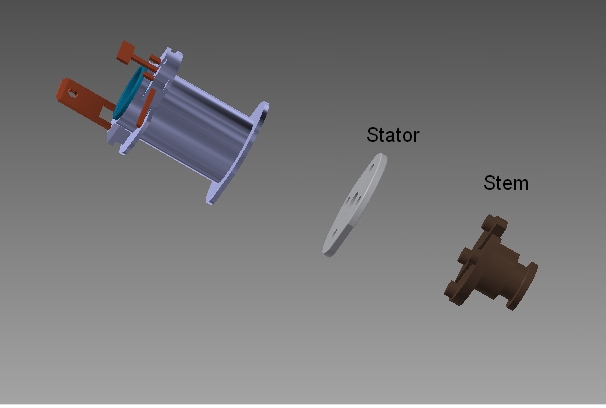 |
The complex part is produced with the above processes, but has the higher cost and worse geometrical tolerance. | 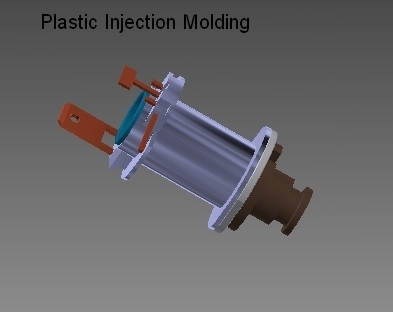 |